Research areas (Selected projects will be shown in the near future):
Thermomechanical Processing of Lightweight Alloys
In this area, we are using severe plastic deformation processing, more specifically, equal channel angular extrusion (ECAE), to impart lightweight alloys (e.g., Aluminum-Magnesium system) with large shear strains to modify and refine the underlying sub-structure. The research entails controlling the processing conditions, mainly temperature, extrusion rate, and imposed hydrostatic pressure to manipulate the evolution of the microstructure. At moderate temperatures, as deformation mechanisms change, the ECAE process introduces a large number of point and line defects (vacancies and dislocations) in the deforming material, causing physical changes to occur. These include the formation of new grain boundaries, grain refinement via dynamic recovery and recrystallization, which compete with alternative deformation mechanisms, such as twinning, and thermally activated processes including the migration of atomic species and precipitation of new phases. We rely on microscopic analyses and thermal property measurements to elucidate key aspects of the microstructural refinement process.
Mg-Al Alloy System
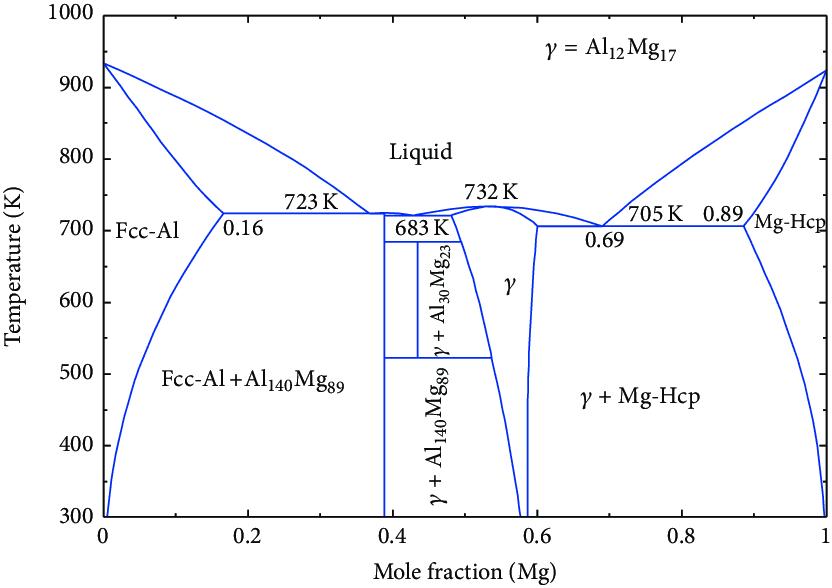
Mechanism-Based
Deformation Behavior
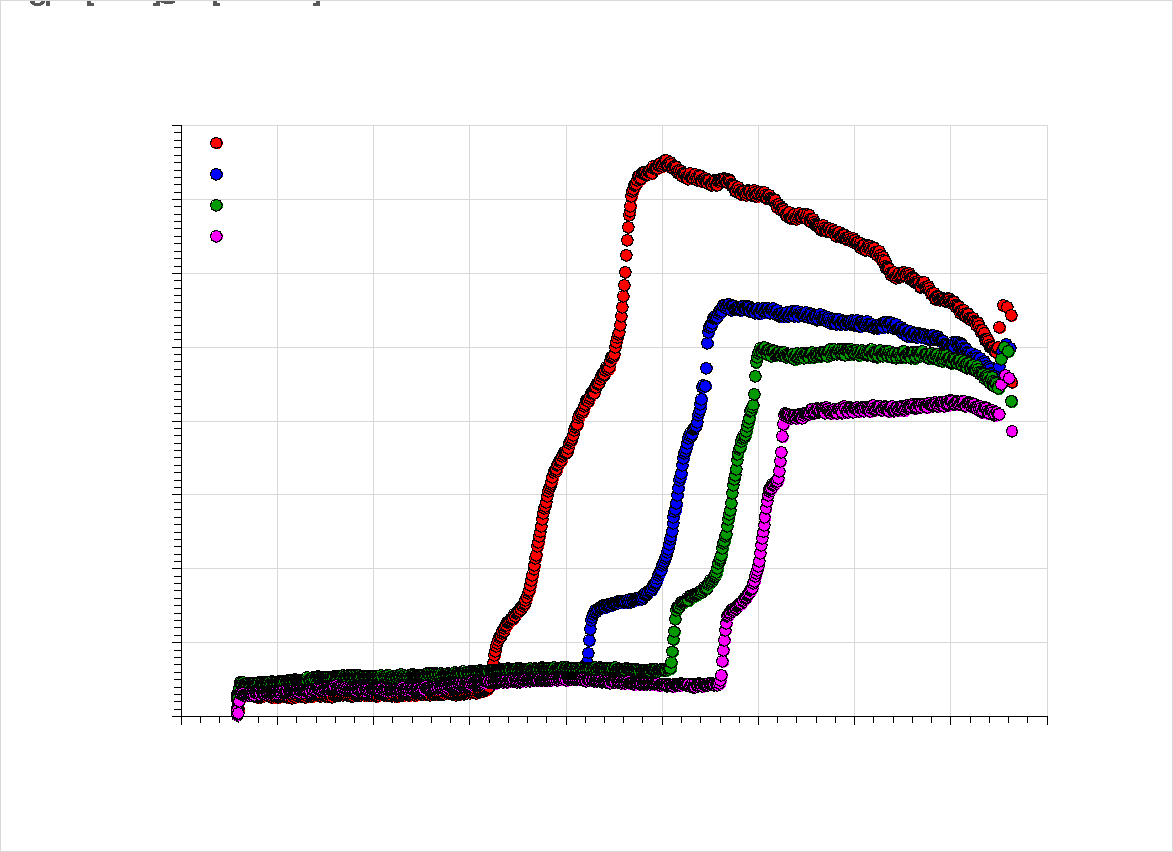
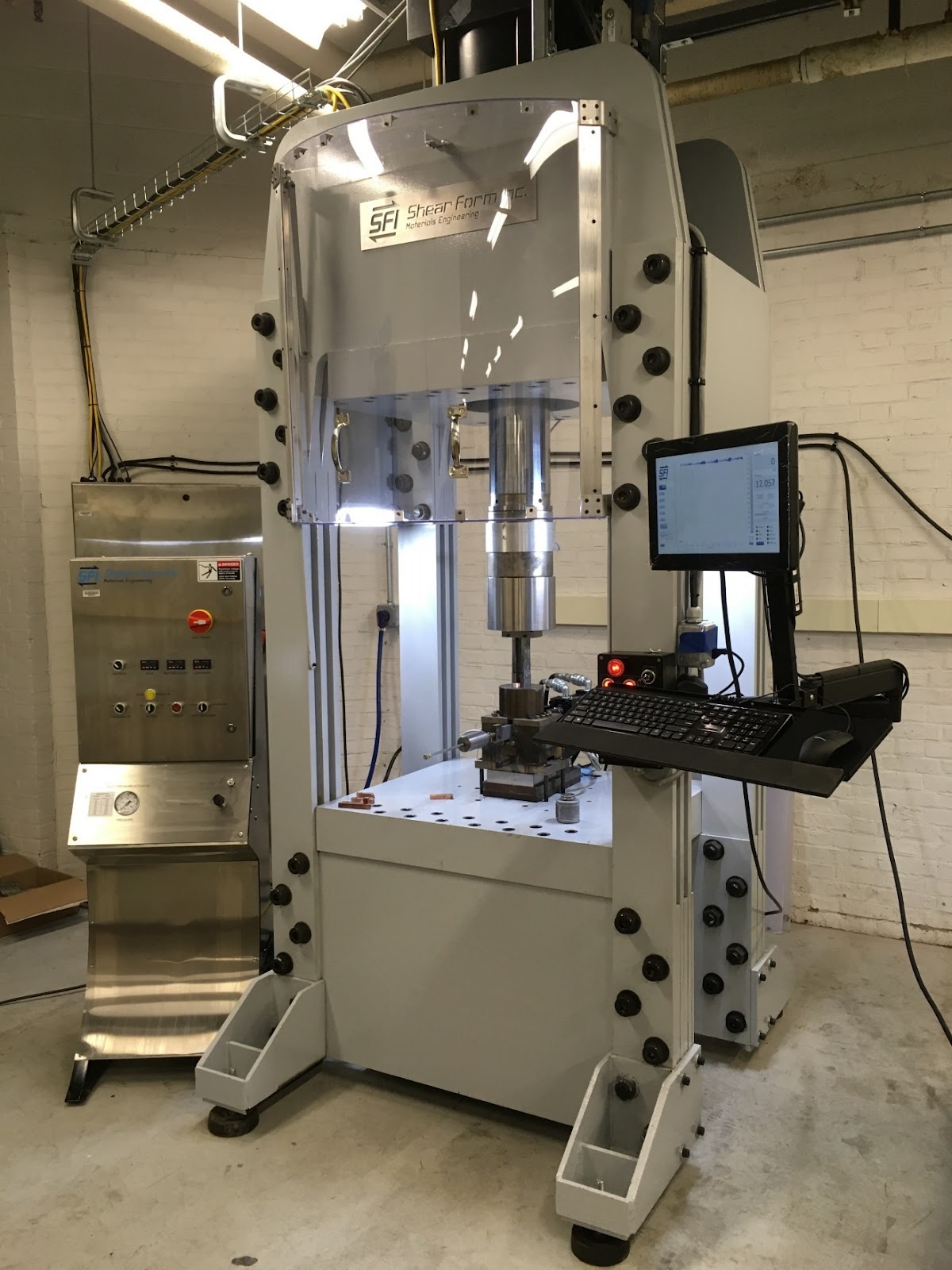
Equal Channel Angular Extrusion
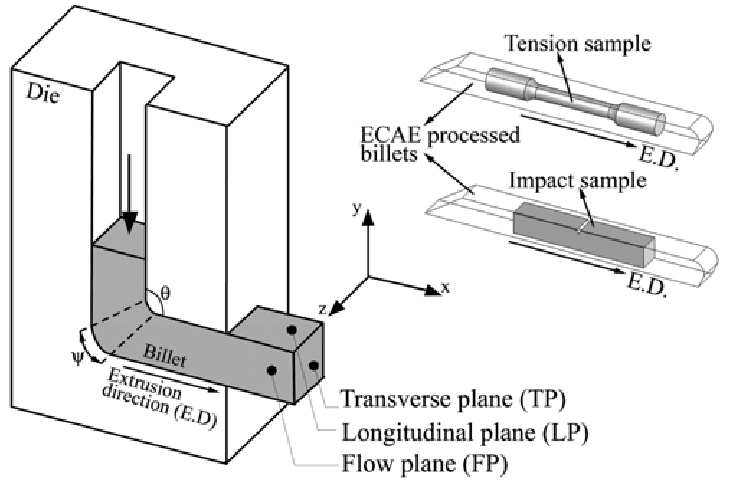
Material Properties
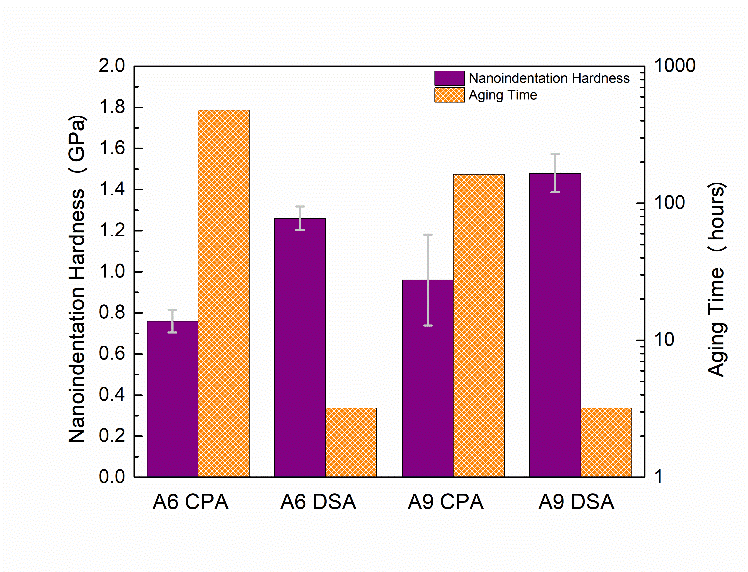
Meso-Structure Modification of Reactive Materials
In this area, we study the fundamental properties of structural reactive materials that enhance and alter the total and rate of energy released during high-rate impact conditions. Under impact, excess strain builds up at the interface between the reactive components, which leads to asperities or hot spots that can lead to an autocatalytic combustion process. By manipulating the topology and morphology of the precursors in the reactive material, significant changes can be imparted to the sensitivity of the material when it is initiated. Our experiments entail studying the coupled effects of slight changes in the precursor composition and the level of their intermixing on hot-spot initiation characteristics. We quantify their quasi-static and high-strain-rate behavior under controlled loading conditions that include both compression and shear. Thermal analysis of representative samples, coupled with post-mortem examination of recovered fragments provide insight into the relationships between the rate of ignition and number of hot spots.
High-Energy Ball Milling

Equal Channel Angular Extrusion
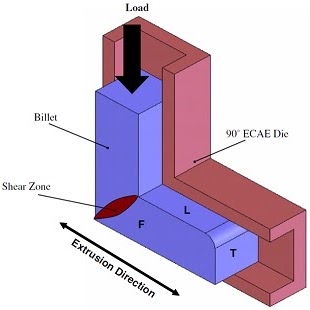
Rotary Swaging
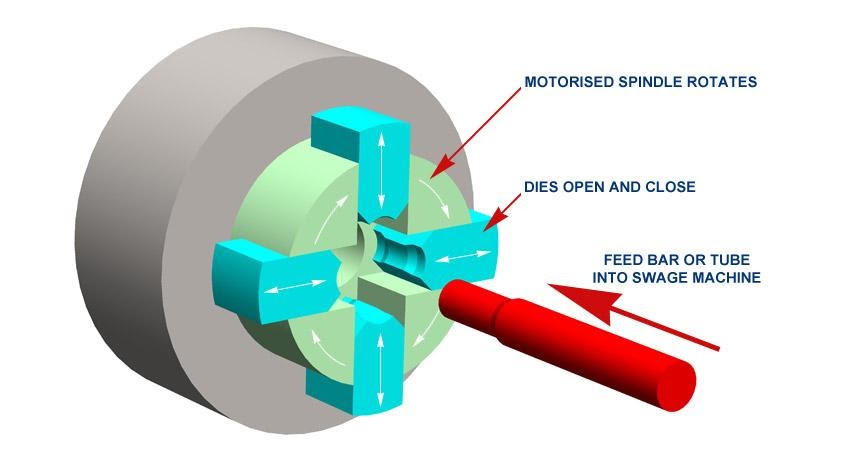
Morphological and Topological Changes affect Structural Properties and Impact Sensitivity
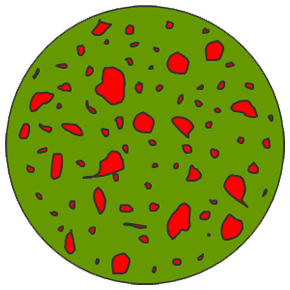
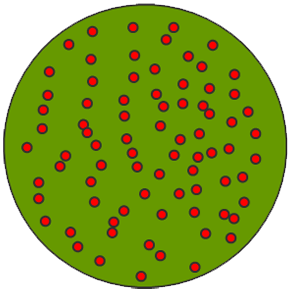
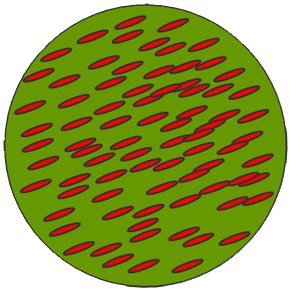
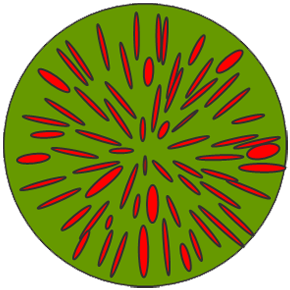
Additive Manufacturing of Refractory Alloys
In this area, we study fundamental processes that occur during laser and electron powder bed fusion processes, two widely used additive manufacturing methods, of refractory metals and alloys. After designing the alloy chemistry, our investigations look at improving the role of process variables that lead to improved and finer-scale control of the microstructure and the resultant mechanical properties. In particular, we vary the rate of heating and cooling by altering the energy being deposited into the material, and the subsequent cooling rate to temper and mitigate the build-up of residual stresses that would otherwise lead to a degradation of key structural properties. Additionally, we control ambient conditions such as the base temperature of the build and/or the level of impurities, e.g., oxygen, during the build process to alter the product properties. These properties are determined via the examination of the morphology, texture, and mechanical behavior.
Deformation Engineering
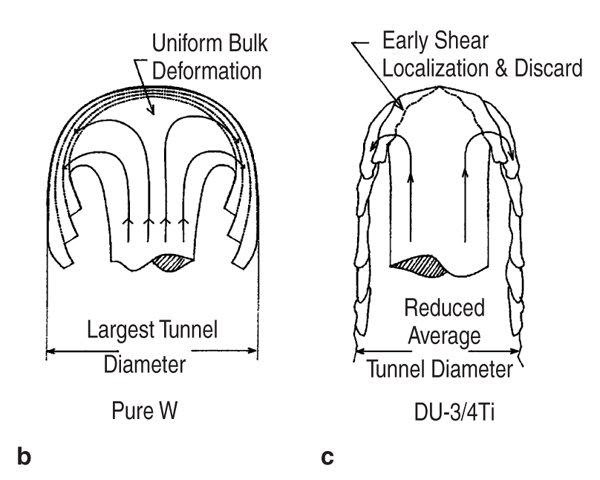
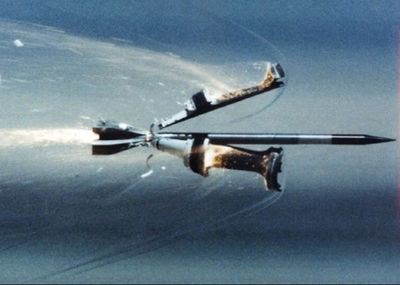
Laser Powder Bed Fusion
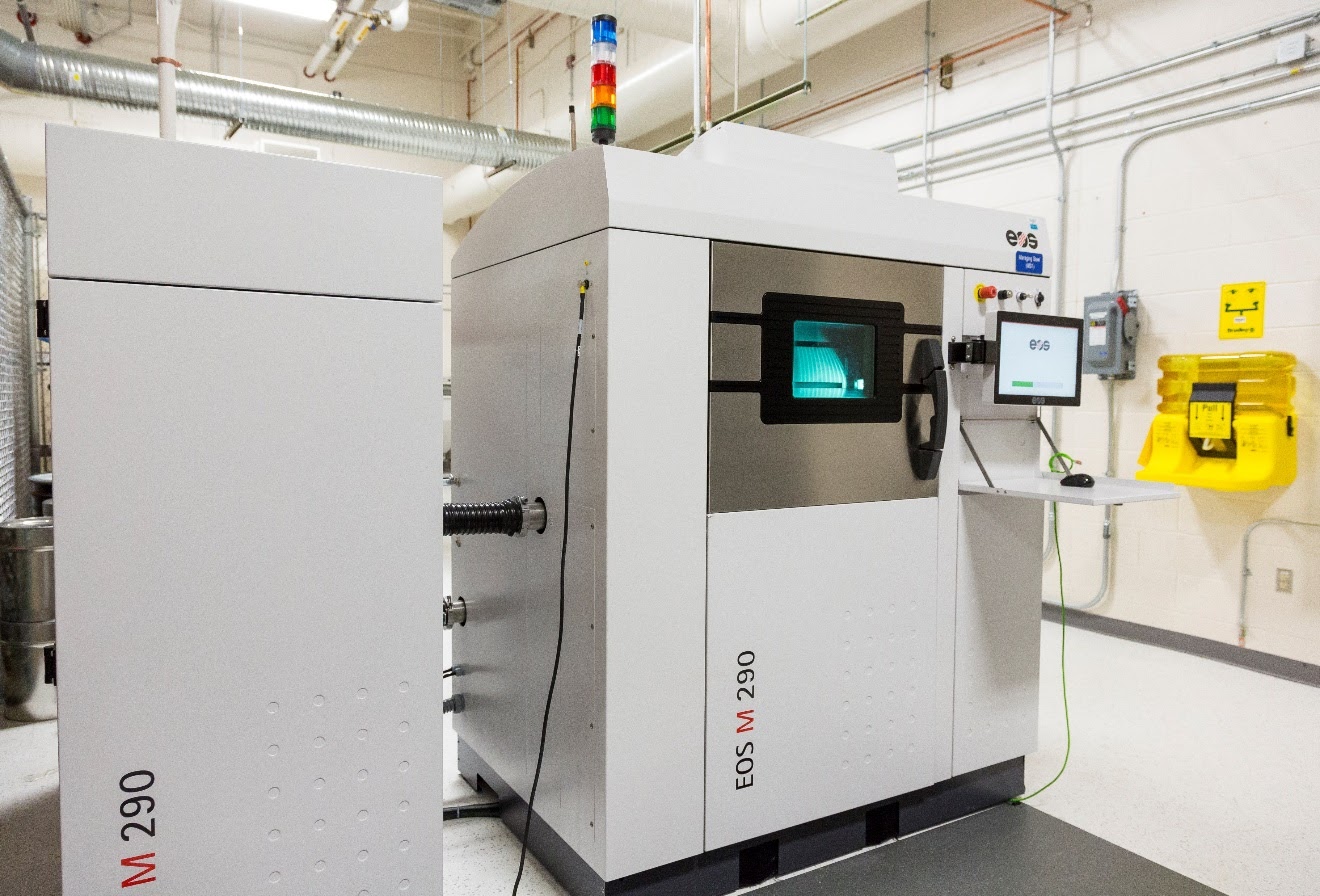
Alloy Design
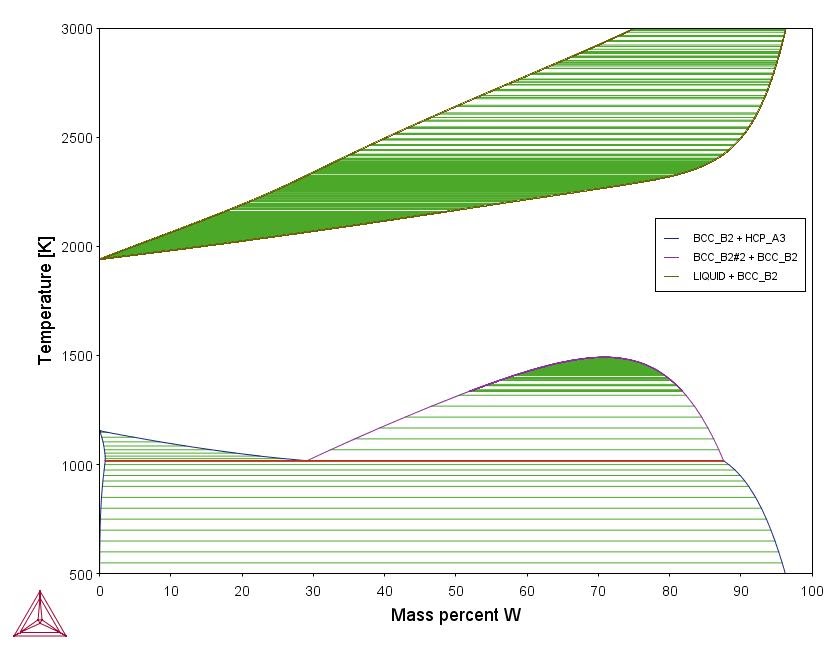
Property Characterization Mechanical
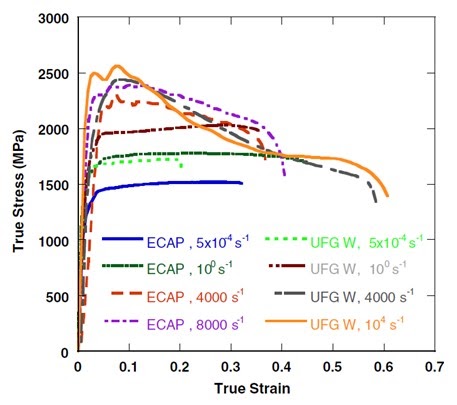
Property Characterization Microstructural
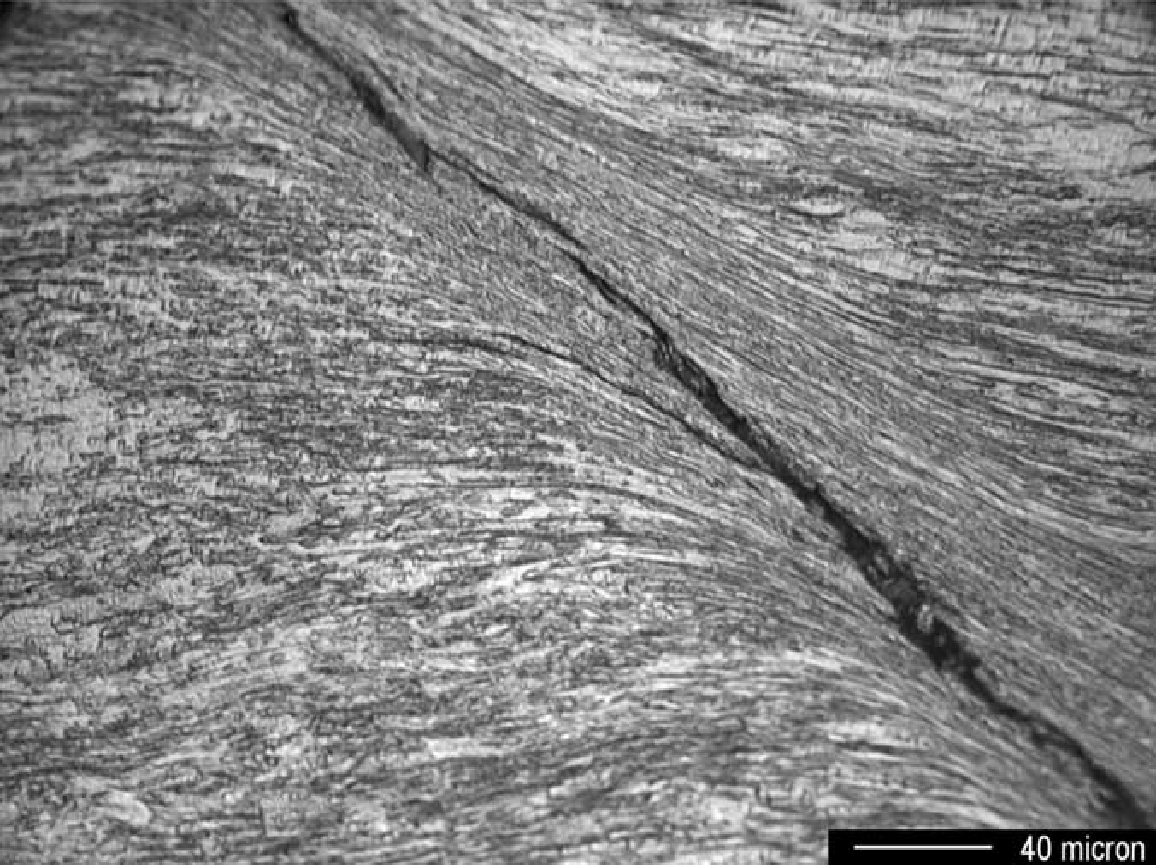