Blink and you’ll miss it: an array of flickering dots, each one mere microns wide, represents the lightning-fast expansion of a crack in glass as a barely perceptible shimmer.
Using an instrument and approach typically used in medicine and astronomy, a team of Hopkins Extreme Materials Institute (HEMI) researchers has tackled a longstanding challenge in fracture mechanics: understanding and quantifying the behavior of fast cracks in brittle materials like glasses and ceramics.
Led by postdoctoral fellows Liuchi Li and Velat Kiliç, the team used Shack-Hartmann wavefront sensing (SHWFS)—a decades-old method for detecting ophthalmic problems and correcting distortion in telescope images—to map changes in shape and movement that happen in material surrounding rapidly spreading cracks with much higher precision and on much faster timescales than ever before. Their approach appears in Mechanics of Materials.
“Can we make glass that won’t crack? How can we make materials last longer? Once cracking begins, how can we prevent a structure’s total failure? Our unconventional use of this old method enables scientists to tackle these important questions,” said Li.
Making stronger, more resilient glass requires a better understanding of stress intensity factors (SIFs) in highly brittle materials. A measure of stress around or near a crack or flaw in a material, SIFs allow scientists to quantify and predict how cracks evolve. In brittle materials, deformations are very small and the speed at which the ends or edges of cracks as they spread are high, making SIFs difficult to determine using direct measurements.
While theories and simulations allow scientists to predict SIFs, high-resolution experimental data has so far been scarce. One established method, digital image correlation (DIC), can sometimes miss small changes. Another, digital gradient sensing (DGS), is better at tracking those small changes but does not capture as much detail.
Mark Foster, co-author and associate professor of electrical and computer engineering, suggested the team explore SHWFS as a way to map both overall changes and small details in brittle materials under stress.
“Shack-Hartmann wavefront sensing seemed like the ideal solution due to its ability to directly measure surface profiles with high spatial resolution. One thing that is particularly unique here is that we are implementing wavefront sensing at extraordinary frame rates to capture the SIF information,” said Foster.
Both DGS and SHWFS use light to measure surface deformation. However, the Shack-Hartmann sensor used by Li and his colleagues has a spatial resolution of about 10 microns—a hundred times better than the resolution typical of conventional DGS. (For reference, a single human hair has a diameter of around 50 to 100 microns.) This allows the team to get remarkable data about behavior near the crack tip, even though it is moving at hundreds of meters per second.
The team’s SHWFS setup, pictured below, uses a series of lights, lenses, and cameras to transform beams of light into an array of dots. As a crack spreads through a sample, the dots in the array change position slightly, representing changes in the sample’s surface slope. The team compared their results to full-scale 3D finite element simulations to verify their method and experimental measurements.
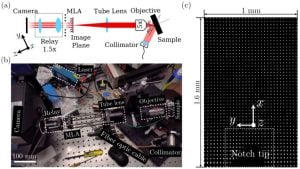
The team’s SHWFS setup (figures a and b) focuses beams of light through a microlens array to provide an average slope of the sample’s surface over a given area. These slope measurements are represented by an array of dots (figure c), which is captured as a series of images by a camera. As the sample cracks, the dots shift slightly to reflect deformations in its surface. A computer program developed by Li computes the shifts in each dot’s position from one snapshot to the next.
“Our method’s unprecedented spatial resolution allows us to probe fundamental questions in the fracture mechanics of brittle materials, opening the door for predictive dynamic fracture theories for engineering applications,” said Li.
The researchers say that their method could not only inform guidelines for civil engineers but also help in the development of novel materials for consumer electronics and in the defense and aerospace sectors.
“An important next step is to integrate SHWFS with complementary techniques,” says Todd Hufnagel, co-author and professor of materials science and engineering. “For example, x-ray phase-contrast imaging (XPCI) can reveal the precise shape and orientation of the propagating crack tip. The combination of the two techniques will give us unprecedented insight into the nature of dynamic crack propagation in brittle materials.”
Team members included researchers from the departments of Electrical and Computer Engineering, Materials Science and Engineering, and Mechanical Engineering at the Whiting School. In addition to Li, Foster, and Hufnagel, authors include KT Ramesh, Alonzo G. Decker Jr. Professor of Science and Engineering, and HEMI postdoctoral fellows Milad Alemohammad and Lei Yang.
ACKNOWLEDGEMENT STATEMENT:
This project was sponsored in part by the Department of Defense, Defense Threat Reduction Agency under the Materials Science in Extreme Environments University Research Alliance, HDTRA1-20-2-0001. It was also supported in part by the Corning Research and Development Corporation.