To stay at the cutting-edge of exploratory science related to materials in extreme environments, the MSEE URA is constantly searching for state-of-the-art equipment, facilities, and tools to expand our research capabilities. However, due to the often-immense cost, long lead times, and laboratory space required for capital equipment and facilities, our ability to acquire new experimental and computational tools are limited.
Thanks to support provided by DTRA and external sources, such as U.S. Congress and the Defense University Research Instrumentation Program, our core research partners have the opportunity to establish novel facilities and equipment for the benefit of MSEE research. Given the collaborative nature of our alliance, most of these facilities and equipment are available to all MSEE partners. Some of these items, like our unique diagnostic tools and small experimental chambers, are shared across the alliance and implemented at multiple partner sites. Below is a listing and description of some of the novel equipment, facilities, and tools, supported through the MSEE URA program.
Johns Hopkins University:
Multi-spectroscopic characterization system
FTIR Spectrometer (Right) and custom dual-spectrometer setup comprised of PRiMIRS and TDLAS (Left). These three spectrometers in conjunction create a multi-spectroscopic system to evaluate composite metal powder performance on Chemical Weapon Agent (CWA) defeat applications with substantial flexibility to investigative needs. PRiMIRS and TDLAS provide a unique capability to assess prompt defeat of CWA Simulants as a function of particle chemistry and thermal behavior and operating on the order of 100 Hz kHz. FTIR provides a greater wavelength range and resolution for a more robust analysis of CWA simulant decomposition products, providing validation to measurements obtained through PRiMIRS, and improved capabilities for quantifying defeat at moderate timescales spanning seconds to minutes, timescales where relevant defeat from a chemical standpoint may be notably unique from thermal.
Ultrasonic Atomizer
The Amazemet Ultrasonic Atomizer is equipped with both plasma and induction melting modules that possess a unique capability to produce powders of almost any metallic alloy. Induction system is suitable for low melting point materials like Al/Mg alloys. The plasma system is used for high melting point materials like refractory alloys, Ti, V, W-based alloys etc. The powder particle size distribution can be controlled by adjusting the ultrasonic frequency (20 kHz: d50 = 60-100 µm; 40 kHz: d50 = 45-60 µm; 60 kHz: d50 = 32-38 µm). This system will generate variety of alloyed reactive powders to optimize and obtain exceptional ignition and combustion properties. The tool is also capable of producing buttons/ingots by alloying and casting.
Physical Deposition System for energetic materials
The physical deposition system, also referred to as a sputter chamber, enables DC magnetron sputtering with up to four guns. With a volume of 18,000 in3 (~300 L), this system can deposit films and powders over eight substrates on the central carousel totaling an area of roughly 4400 cm2. Ranging from nanometers to microns thick, we can precisely control the composition and film microstructure within a single deposition. The system can deposit compositionally graded samples onto a variety of substrates through custom shielding and target design. This makes the sputter chamber an ideal tool for combinatorial studies of reactive and structural materials. These materials are used in various experimental tests to characterize the effectiveness of combustion and efficacy of their defeat of chemical and biological warfare agents.
Metal Extrusion Additive Manufacturing (MEAM) system
Conventional 3D printing of metallic structures (laser powder bed fusion, LBPF, or direct energy deposition, DED) relies on laser melting of powders. While effective with many structural materials, LBPF/DED of reactive materials (RMs) can be very challenging given the propensity of the RMs to oxidize and evaporate during laser melting. To overcome these challenges, we have purchased a liquid metal extrusion system that operates at much lower temperatures and uses metallic wires as feedstock instead of reactive metal powders that can be difficult to handle.
In this effort we will demonstrate the ability to print solid and porous reactive metal structures that possess strength, toughness, and reactivity. The first year will focus on establishing printing capabilities and protocols using a nonreactive Zn alloy and a reactive Al alloy as model materials. Subsequent efforts will expand to other alloys based on feedback from the reactive alloying efforts elsewhere in RA2. Strength and toughness will be tested within this effort and reactivity will be tested within RA3.
Flash X-ray Diagnostics for Analysis of High-Speed Impact and Penetration Events
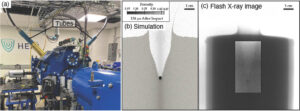
Figure 1 – (a) Two flash X-ray tubes are pictured, supported by brass mounts, emerging from the sides of the impact chamber of a two-stage gas gun in the Johns Hopkins University’s Hypervelocity Facility for Impact Research Experiments (HyFIRE). These flash X-ray tubes enable acquisition of images visualizing the internal processes in a material during impact and penetration. This information is critical for developing and validating robust predictions of these processes through computational modeling. (b) An example numerical simulation of a steel projectile shot into a bed of sand at 1.5 km/s. (c) An example of a flash X-ray image of a steel projectile penetrating into a bed of sand, providing validation to the model predictions shown in (b). https://doi.org/10.1016/j.jmps.2024.105644
High-velocity impact and penetration involves material failure and spallation at microsecond timescales. Visualizing and quantifying the progression of the impact and penetration process is critical for developing robust predictions of their effects. Congressional funds enabled the acquisition of new flash X-ray tubes compatible with JHU’s existing L3 flash X-ray system. These tubes have enabled us to continue to view through materials experiencing impact and penetration, revealing the temporal evolution of internal craters and damage processes. This information is being used to validate numerical simulations of the penetration process in materials such as sand, sandstone, and concrete. Figure 1 illustrates the flash X-ray tubes mounted in the impact facility at JHU, as well as an example of a comparison between model predictions and flash X-ray images.
High-Pressure Triaxial Compression Instrument
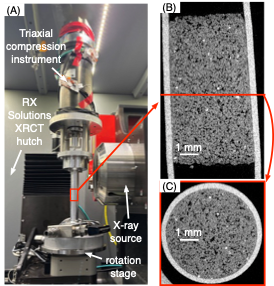
Figure 2 – (A) Triaxial compression instrument installed in an X-ray computed tomography (XRCT) facility at JHU. (B) Example cross-section of a 3D X-ray image of a sandstone sample imaged while under compression. (C) Another cross-section through the same sandstone sample shown in (B).
During impact and penetration, geomaterials such as sand, rocks, and concrete experience very high pressures. Understanding the mechanical response of these materials to such high pressures in the absence of dynamic loading is the starting point for constructing numerical models used to predict their response to impact. Triaxial compression instruments are a conventional means of measuring the stress and strain response of materials subjected to high pressures. Designing these instruments to operate within X-ray computed tomography (XRCT) facilities which enable acquisition of 3D images of the material before, during, and after the high-pressure loading is particularly novel and useful for developing and validating numerical models of material behavior. DURIP funds enabled design and construction of a novel high-pressure triaxial compression apparatus allowing us to visualize the deformation of sand, rocks, concrete, and other geomaterials while they are subjected to up to 200 MPa of hydrostatic confining pressures and up to 2 GPa of axial stresses. This is the only such instrument to enable imaging at such high pressures and it provides a unique opportunity to directly observe and quantify the processes occurring within materials as they are subjected to extreme pressures. The data is being used to calibrate material response in numerical simulations of impact and penetration. Figure 2 shows the instrument and example images of sandstone.
University of California Riverside:
Multi-Camera Spectroscopy and Pyrometry (MCSAP) system
MCSAP is an experimental system designed for high-speed imaging and temperature diagnosis of composite combustion reactions. This setup combines two imaging arms: one for capturing RGB video of the reaction scene and another for obtaining spatially resolved spectra of burning composites. The RGB arm, featuring a color camera, measures condensed-phase temperatures using three-color pyrometry. Meanwhile, the spectroscopic arm passes light through a mask with narrow slits, dispersing it with a diffraction grating to collect spectral data with a monochrome camera. This system allows measurement of both gas and condensed phase temperature and provides insights into complex and dynamic combustion processes.
Transmission electron microscopy system with Atmospheric cell
The Transmission electron microscopy (TEM) is a microscopy technique in which a beam of electrons is transmitted through a specimen to form an image. The specimen is most often an ultrathin section less than 100 nm thick or a suspension on a grid. An image is formed from the interaction of the electrons with the sample as the beam is transmitted through the specimen. The addition of atmospheric control allows us to heat samples during the microscopy process.
University of California San Diego:
Laboratory for Laser Ablation Plasmas and Shocks (LAPS)
The Laboratory for Laser Ablation Plasmas and Shocks (LAPS) in High Energy Density Physics group consists of a variety of lasers, with various energies, pulse lengths and wavelengths including 40J, 1 μm, 12 ns amplitude and 4.5J continuum laser with 6 ns, 532 nm lasers to study laser energy absorption, ablation and thermomechanical shock generation in solid, tamper and high density foam targets. Several lasers ranging from 10 J to several 100 mJ with varying pulse length are available for optical diagnostics including interferometer, Streak Optical Pyrometry (SOP) and Optical Thomson Scattering (OTS). High resolution optical and Extreme Ultraviolet wavelength spectrometers (resolutions of <0.05 nm and < 0.01 nm for wavelength range of 7 to 70 nm and 2 to 20nm, respectively) are available to diagnose EUV sources. In addition, we have high repetition rate Spectrograph (10 Hz continuous operation and 40 Hz burst mode) and an Optical Streak Camera (temporal resolution of ~10 ps with sweep time of 0.5, 1, 2, 5, 10ns/15mm). Faraday cups are available to detect ions and electrons produced in laser plasma interaction region. The cutting-edge lasers and pertinent diagnostics facilitate unique hands-on experience to undergraduate and graduate students and postdoctoral scholars.
University of Illinois Urbana Champaign
Fast Infrared Diagnostics in the Fingerprint Region
Work on agents and simulants has highlighted the need for fast infrared diagnostics that exceed FTIR capabilities (~150 Hz maximum) in the key 8-12 micron fingerprint region. For this application a newly available Telops infrared camera was purchased, allowing 10kHz spectra in the long wave infrared (LWIR) region to be obtained in our facilities. We simultaneously developed a fast (f/2) LWIR dispersive spectrometer to couple to the camera system. This combination allowed spectra to be taken at 3 wavenumber resolution with exposures of 100 us. This represents a huge jump in ability to monitor agent surrogate concentrations in the shock tube and explosion test facility on timescales relevant to prompt agent defeat. The figure below at right shows a spectrum, and the figure at left shows the camera and spectrometer in the field at the Nevada National Security Site. A second camera for fast near-infrared (NIR) spectroscopy was also purchased (middle system in the figure at right), enabling complimentary measurements of agent decomposition products.
Large Test Chamber and Associated Infrastructure Improvements
One of UIUC’s unique capabilities is large scale explosives testing, and under this award UIUC purchased a 700 liter hermetically sealed chamber system for operation in both agent defeat and actinide-containing systems. This system will enable testing at the 50gram scale of high explosives with agent surrogates, as well as tube collapse (Koski-tube) experiments scaled up 10x from current experiments. To accommodate this chamber and enable year-round testing at the remote explosives testing site, we added significant site improvements to electrical, mechanical, and environmental systems at the site, including insulation, HVAC, and added storage. Optical tables and support systems were put in place to allow framing, streak, and high speed cameras to be applied to the new chamber system, as well as spectroscopic diagnostic. The image below highlights some of these infrastructure improvements. These improvements and the new chamber allow UIUC to have perhaps the only university facility for year-round, mid-scale explosive testing in agent defeat and actinide-containing systems.